In the current fast-paced manufacturing landscape, organizations are always looking for ways to optimize production processes and cut time-to-market. One approach that has drawn significant attention is quick injection molding, an innovative method that offers manufacturers a distinct edge. By bridging the gap between prototype development and full-scale production, rapid injection molding empowers businesses to produce high-quality parts swiftly and with precision, responding to market demands with nimbleness.
This approach not only hastens the development process but also significantly minimizes costs related to traditional manufacturing methods. With the ability to swiftly produce complex designs in a variety of materials, rapid injection molding permits businesses to validate their ideas in live scenarios and make necessary adjustments without the lengthy delays usually connected to conventional molding. As industries develop and consumer expectations heighten, adopting rapid injection molding can be the game-changing strategy manufacturers need to maintain their lead.
Advantages of Fast Injection Molding
Fast injection offers considerable advantages for manufacturers looking to streamline their production methods. One of the primary advantages is quickness. This approach reduces the duration it requires to create forms and produce parts, allowing firms to launch products to market significantly quicker than traditional injection methods. The faster turnaround times allow businesses to react to market demands and trends more effectively, giving them a competitive edge.
Another key benefit is cost efficiency. While the initial investment in quick molding may be higher, the overall benefits arise from lower lead times, lower labor costs, and less material waste. By improving the manufacturing system, companies can reduce their overhead and maximize profit margins. Furthermore, the capability to create small batches without incurring significant additional costs makes this approach perfect for startups and little businesses that need to control their finances carefully.
In conclusion, rapid molding allows greater development freedom. Producers can refine designs quickly, enabling for more innovative product development. This adaptability ensures that changes in designs or needs can be executed with little interference to the manufacturing timeline. As a result, producers can constantly refine their products and stay ahead of their rivals by offering higher quality and customized solutions tailored to client requirements. ###
Quick form has found a niche across multiple of industries , greatly improving manufacturing efficiency and rapidity. Within automotive manufacturing, producers utilize this technology to create sophisticated elements with exceptional accuracy. This technology facilitates quick prototyping and small batch production, permitting companies to test prototypes and iterate swiftly bypassing the long lead times typically associated with conventional molding techniques . With the evolution of automotive designs, the ability to manufacture parts quickly becomes critical for staying competitive in the market .
The healthcare equipment industry also enjoys significant advantages through rapid molding technology. With stringent regulations and the need for high-quality standards , healthcare producers employ this method to create prototypes and finished goods effectively. Rapid injection molding enables the swift creation of minute, detailed elements such as injectables, implants , and healthcare devices. The capacity for production these parts at a quick speed helps firms launch new innovations to market rapidly , which is crucial in a field that advances rapidly and requires timely solutions to rising medical challenges.
In consumer goods , this technique plays a key role in creating products that meet ever-changing market trends. Businesses utilize this technique to develop prototypes that can be evaluated and modified before mass production. By minimizing the time it takes to move a product from concept to shelf , this method enables businesses to respond to customer expectations dynamically . This flexibility in production boosts customer satisfaction but also provides a position of strength in a market defined by constant innovation .
Future Trends and Innovations
As the a manufacturing landscape changes, fast injection molding seems to be poised to play a significant role in driving productivity and creativity. One of the most important trends is the rising integration of automation and automated technologies in the injection molding process. Automated can boost accuracy, cut down on cycle times, and minimize human error, leading to a smoother production workflow. This not only boosts output but also allows manufacturers to respond faster to market demands, making rapid injection molding an a competitive advantage.
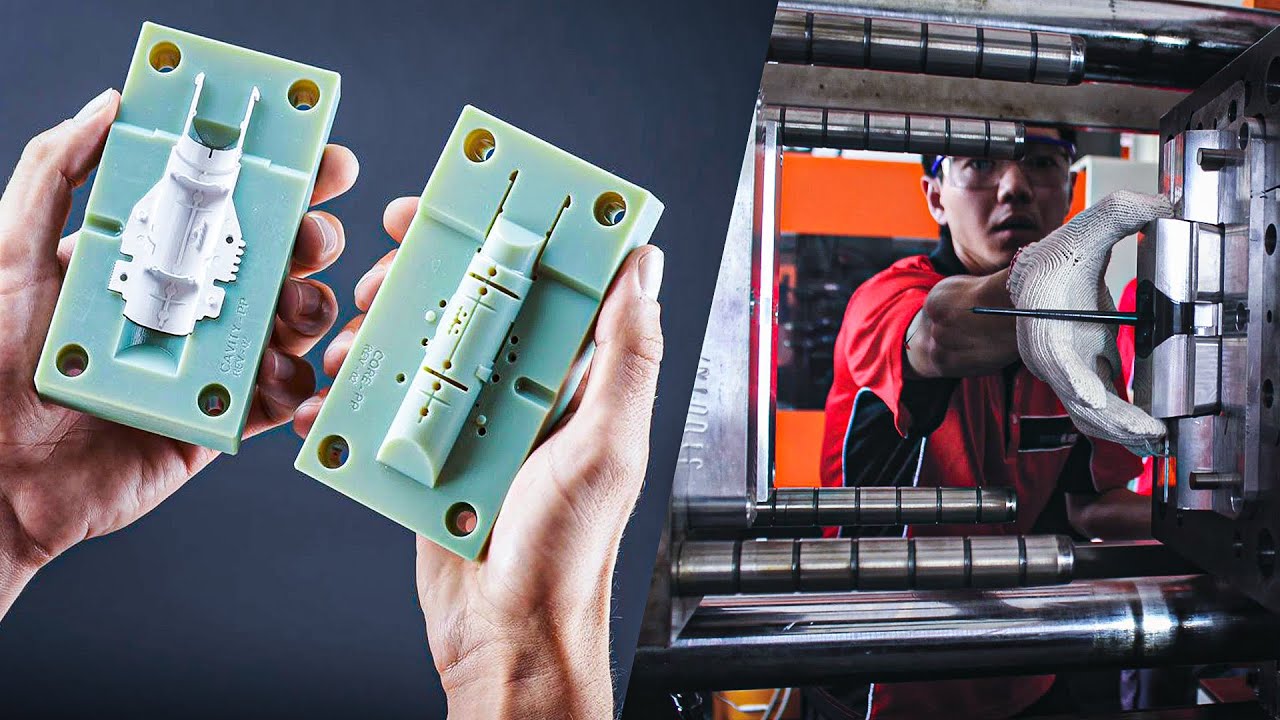
Another noteworthy trend is the advancement of advanced materials specifically designed for rapid injection molding. Innovations in polymer science are resulting in the creation of materials that offer improved strength, flexibility, and thermal resistance. These new materials enable manufacturers to produce more complex and durable designs, opening up opportunities for new applications in industries such as the automotive sector, aviation, and consumer electronics. As material capabilities advance, rapid injection molding will continue to evolve, providing enhanced solutions tailored to specific industry needs.
Furthermore, there is a increasing emphasis on sustainability within the rapid injection molding sector. Manufacturers are progressively seeking ways to reduce waste, utilize recycled materials, and minimize energy consumption during production. This transition towards eco-friendly practices is not only a response to consumer demand but also a strategic move to meet global sustainability goals. By implementing sustainable practices in rapid injection molding, companies can boost their brand reputation while maintaining effective and advantaged manufacturing processes.